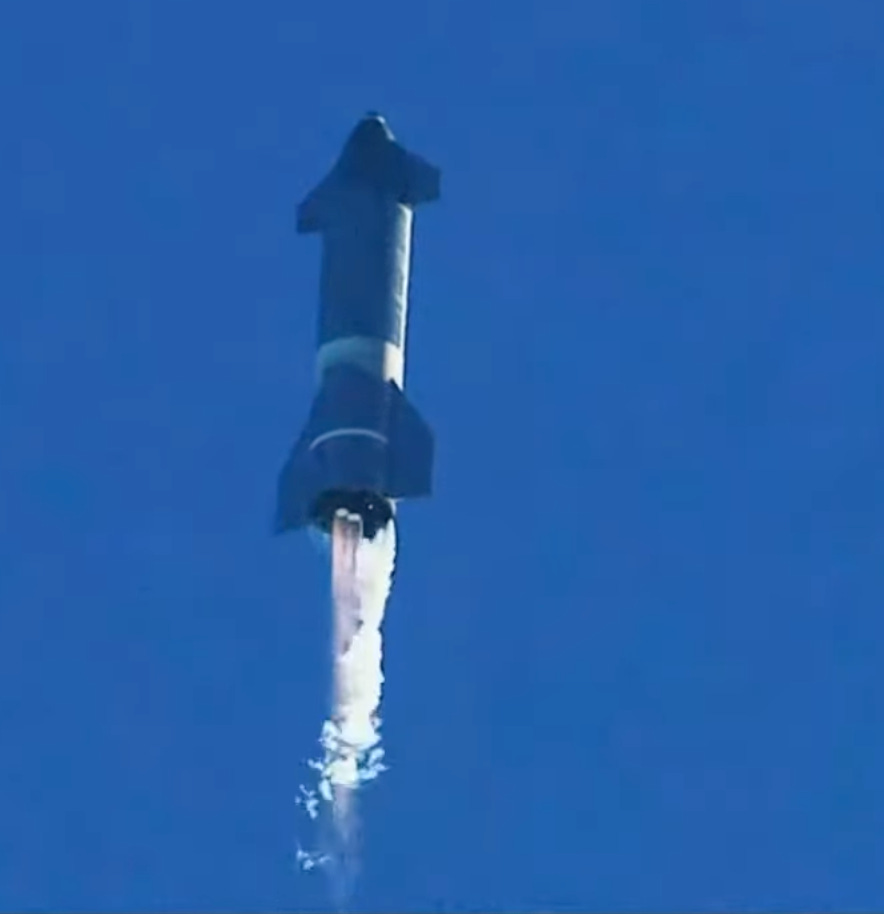
On December 9th, 2020 SpaceX launched the first high altitude test flight of Starship, the fully reusable upper stage of their heavy fully reusable launch system. Before the flight, SpaceX founder and Chief Engineering Officer Elon Musk stated his estimate of the chances of success were 1 in 3, which seemed reasonable given the many firsts that would need to occur - The first launch using three liquid methane-liquid oxygen (methalox) fueled Raptor rocket motors; first flight above 300 feet; first sustained burn of three Raptors; first in-flight sequential shutdown of individual Raptors; first pitch over into aerodynamic horizontal belly-first “skydiver” descent using the unique moving control surfaces the internet has dubbed “Elonerons”; first descent managing cross-range to accurately arrive at the landing pad; First Raptor inflight relight; first thrusting pitch up from slightly nose down to vertical landing attitude; and first propulsive vertical landing after unpowered descent.
In the end, only that last item was not completed successfully due to insufficient pressure in a header tank used to fuel the rockets for landing, per a post-flight tweet by Elon Musk, which provided insufficient pressure to sustain all required Raptors for the landing burn.
And all of this testing of unproven hardware was performed in the bright winter Texas sunshine in view of thousands of people, with multiple SpaceX cameras streaming the entire test over the internet to hundreds of thousands of viewers.
The SN8 test flight achieved most but not all of the objectives, but as a test, it was completely successful. Any engineer will tell you that more is learned from test failures than from successes, especially for a complex system. After all, you can’t fix what you don’t know is broken, and you can’t possibly know everything that needs to be fixed, so the best way to find out what to fix is to try to break as much as possible in testing.
In a shorter version, breaking things in a test is what tests are for.
SpaceX takes a page from the various iterative design techniques, such as those developed for the software development world, embracing a build-break-improve cycle. Compare this to the traditional cost-plus-contract guaranteed-profit space hardware companies, all defense contractors, who over-powerpoint and over-design and over-simulate and over-analyze in an attempt to design out all possible embarrassing test failures, at the cost of not robustly exploring the unknown-unknown potential operational failures. In that world, negative test results and the resulting negative publicity are to avoided at all costs, as they may draw unwanted attention from the US Congress and potentially result in derailing the cost-plus gravy train through program cancellation.
If prime contractor Rockwell and NASA had thought to line the inside of the leading edge wing tiles with thin sheets of high temperature resistant stainless steel, the loss of Columbia would not have occurred even with a hole punched through the tile, and if they had robustly tested what would happen if a piece of insulating external tank foam had fallen into the tile (as was done in the post-accident investigation), they very well could have done just that.
But SpaceX is not building Starship under government contract. While the Starship program has recently attracted NASA and US DoD interest in possible applications, including use of Starship in the nascent lunar return program, at base Starship is the result of the application of basic principles by SpaceX: full reusability is the key to reducing the cost of getting mass into Earth orbit; full reusability is not practical to retrofit to any extant launch system including the Falcon 9; lowering the cost per unit mass into Earth orbit is the path to an interplanetary transportation capability; and a robust interplanetary transportation capability is the only way to ensure that humanity becomes an interplanetary species.
The Falcon 9 vehicle has been continuously upgraded, now at the Falcon 9 Block 5 configuration, incorporating minor and major changes to enhance reusability and reliability. Falcon 9 has now launched 100 times, and the Falcon 9 first stage has been successfully recovered intact 68 times.
The payload fairings have also been retrofitted for recovery, now re-entering under attitude control and deploying a steerable parasail for soft landing, either in the ocean for pickup or into the nets of specially outfitted ships. Reportedly each fairing set reused saves SpaceX $3 million.
And as recently as 2017 SpaceX President Gwynn Shotwell stated the company would be attempting a second stage re-entry and landing by 2018, accompanied by rendered imagery.
But retrofitting the ability to recover from orbit and reuse the second stage would come at the cost of extra non-payload weight, which in turn reduces the payload unless performance is increased, and also adds complexity, increasing the risk of failure to successfully perform the primary mission of delivering spacecraft into orbit. And in the end, even with the efficiency and cost benefits from reusability, a fully reusable Falcon 9 launch system would still yield a lift capacity insufficient to accommodate Elon Musk’s overarching goal of making humanity a multiplanetary species through the colonization of Mars.
SpaceX also builds the Dragon series of capsules, which since the Space Shuttle retirement, has provided the only method available to bring significant payload back down to earth from the International Space Station. Cargo Dragon capsules have been lost, some in ground testing and one in a launch vehicle explosion, with fixes implemented and flown. Last year the upgraded Crew Dragon debuted and flew a successful unmanned test flight to the ISS, this spring NASA astronauts Bob Behnken and Doug Hurley famously launched to the ISS and returned safely to splashdown in the final test flight of Crew Dragon, and this fall the first operational Crew Dragon mission launched, with the crew scheduled to remain on the ISS for six months before being replaced in the next Crew Dragon launch.
Note that SpaceX contract for Commercial Crew transport has paid SpaceX about 60% of the amount paid to traditional aerospace manufacturer Boeing for their Commercial Crew vehicle, the CST-100 Starliner. Boeing has yet to complete a single successful unmanned Starliner test flight.
SpaceX has just launched and docked to eth ISS the first cargo space station resupply flight using their new Cargo Dragon 2 capsule developed from the Crew Dragon design, and SpaceX has also won a contract for the Dragon-XL lunar resupply vehicle to transport supplies to the Lunar Gateway station in orbit near the moon, again iteratively developed from the latest Crew Dragon.
But no capsule can transport people to Mars in more than an expeditionary mode - even the NASA Artemis “exploration” capsule will only accommodate a handful of government employee astronauts, in far less space than the cabin of the Space Shuttle, and will require additional habitable volume for a Mars mission.
So recognizing Falcon 9, no matter how reusable, will not provide enough lift capacity to orbit to support colonization, SpaceX has designed a much larger launch system to support their Mars colonization goals. Variously referred to since 2010 as the Mars Colonial Transport, the Interplanetary Transport System, the BFR or Big Falcon Rocket, and finally Starship and Super Heavy, the system was designed to be fully reusable from the start and to deliver a massive 220,000 lbs to low Earth orbit.
Initially designed to be built with the same carbon fiber composites used in the Falcon 9, the new large launch system features a very large first stage, which would recover and land much the same as the Falcon 9 first stage, topped by a combined second stage and space vehicle. Starship would perform the final boost into Earth orbit, deploy payloads for satellite launch, support crew for manned missions, refuel from tanker Starships, re-enter and land on the surface of the Earth, and, refueled, would also be able to travel to, land on and take off from Mars.
The new system would also use a new much more powerful rocket motor, the Raptor, burning cryogenic liquid methane with liquid oxygen (a fuel cycle known as methalox). Methane can be synthesized from Martian undersurface water and carbon dioxide, which makes up most of the Martian atmosphere, and oxygen can be extracted from that same subsurface (not subterranean - submartian?) water. Producing fuel and oxidizer on Mars will eventually enable ships to be refueled using in-situ Martian resources before their return to Earth. By eliminating the need to carry both fuel and oxidizer sufficient for a return trip all the way to Mars, the choice of methalox significantly reduces the lift required for a round trip.
To prove the change from carbon fiber to stainless steel, the inactive and empty SpaceX Boca Chica, Texas SpaceX facility finally saw activity as welders starting to weld up what looked more like an industrial water tank than a space vehicle. Where were the cleanrooms? The multi-million dollar factories? The mountains of paperwork that government functionaries insist actually enable all flight? Initially welded together in the open air, a tripod-legged somewhat wrinkly stainless steel construct took shape, dubbed “Starhopper” by SpaceX fans on the internet closely following the activity in southernmost Texas. Starhopper eventually flew a low altitude 500 ft hover test atop an early prototype Raptor in July 2019.
Multiple test articles and prototypes followed, starting with SN1, some failing to hold sufficient pressure during cryogenic nitrogen pressure tests or collapsing due to test sequence errors, and others failing in spectacular explosive fashion, all bringing to light required fixes. When the SN constructs began passing all their tests, proving successful accumulated design, production, and materials changes, next came a pair of flight test vehicles, SN5 and SN6, flying hover tests in August and September of 2020 that duplicated the Starhopper flight pattern. A set of pressure test tanks labeled SN7 were followed by the first high altitude flight test article, SN8, which flew a 150-meter hover test and then was fitted out with nose cone, a set of those movable “Elonerons”, and three Raptor rocket motors.
The Starship vehicle was designed to fly into orbit boosted by the Super Heavy, and re-enter in a method reminiscent of the Space Shuttle, belly first, with attitude control using reaction control jets until the atmosphere becomes thick enough, and then using those “Elonerons” in a method explained as “skydiver mode”. But the landing will be tail down as with the Falcon 9 first stage, so a final “flip” maneuver using the “Elonerons” combined with vectored thrust from relit Raptors would flip the vehicle from belly-first to tail first and then brake to a soft landing.
The first-ever test of ignition, boost, transition to belly-flop descent using “skydiver mode” aerodynamic control, precise navigation to the landing pad, and the final relight, pitch-up to tail first, and landing under thrust, was the test flight that flew on December 9th. And surprisingly it almost completely worked - only the pressure issue in the methane header tank preventing full thrust from the relit Raptors prevented 100% success and controlled landing on the landing pad.
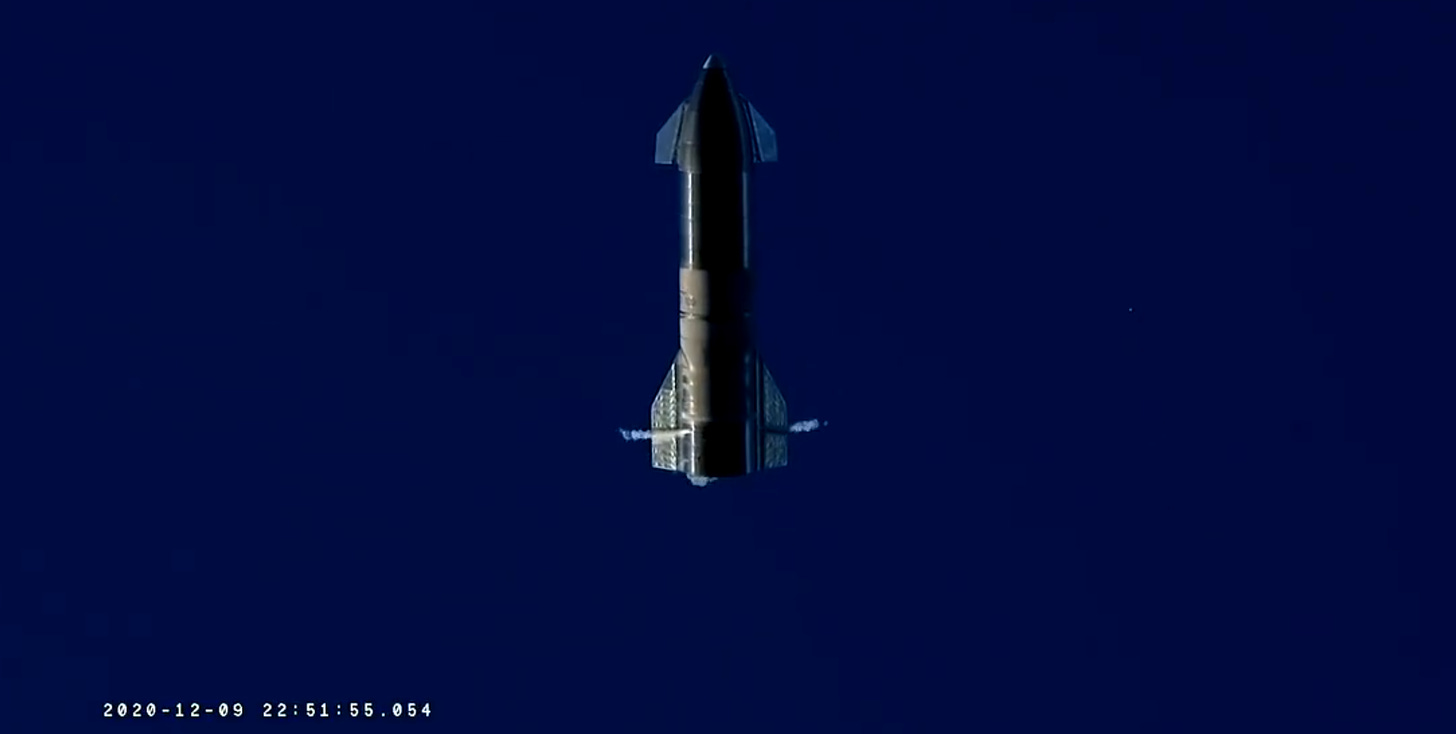
Even with the methane tank pressure shortfall, estimates based on the landing video indicate the vehicle had braked to well under 100mph when it hit the landing pad - after falling from almost 8 miles.
In anticipation of losing a vehicle in this stage of testing there’s another copy in the wings, SN9, which may be rolled out as soon as next week to begin acceptance tests prior to flying another 40,000 test flight, with fixes for the header tank issue and anything else that the volumes of test data indicate needs fixing - that is, a classic-build-test-analyze-build iterative development methodology. The software world has scrums and spirals and other subspecies, but all feature this same iterative build-test-build cycle.
And more are on the way - the activity watchers on the internet, aided by a small coterie of dedicated crowd-funded on-site photographers, live web cameras, and even an aerial photography firm that live-streams weekly overflights, have identified parts being manufactured for at least six more Starships as well as the first Super Heavy booster. Challenges yet to be addressed include finalizing a method for securely attaching heat shield tiles to the downward-facing side of the orbital vehicle, though this is not nearly as critical on a stainless steel skinned starship compared to the low-melting-point aluminum structure of the Space Shuttle, proof of the Starships controllability in a belly-flop orbital re-entry, and the development of orbital refueling, critical for interplanetary use of Starship.
Construction of a massive elevated launch structure and service tower for the Super Heavy+Starship stack also needs to be constructed, and there’s an FAA environmental re-assessment that could complicate progress, but SpaceX’s successful failure on Wednesday highlights just how far the SpaceX team has progressed using iterative design along the path to fulfilling Elon Musk’s ambitious goal of saving humanity from the risks of remaining a single-planet species.